Technical Challenges in Lithium Battery Recycling
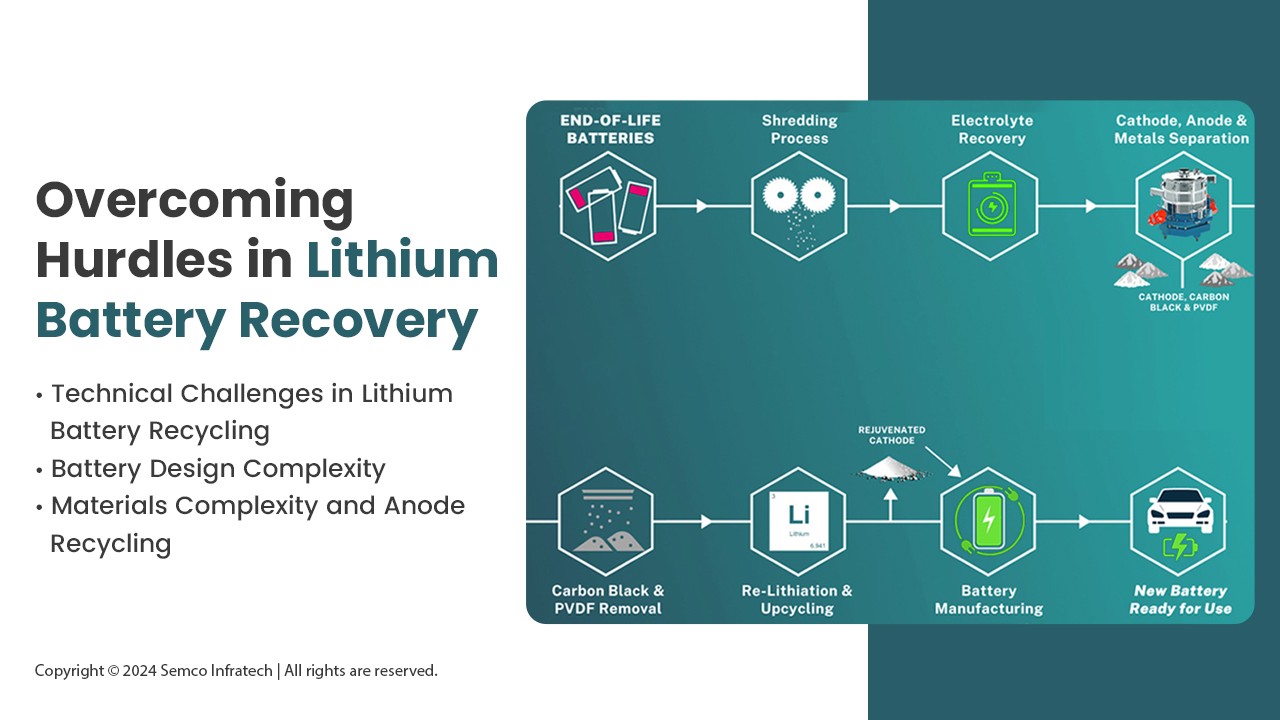
The current landscape of lithium-ion battery recycling technology presents a multitude of challenges that need to be addressed for effective and sustainable solutions. As commercial lithium-ion batteries continuously evolve to achieve higher energy density, longer mileage, and enhanced safety, technical challenges in the recycling process become more prominent.
Battery Design Complexity
The diversity in lithium battery designs, encompassing cylindrical, square, and soft-pack batteries, poses unique challenges in disassembly and pretreatment. With manufacturers exploring innovative structures, recycling processes face difficulties in component disassembly and separation, especially with the absence of standardized designs.
Materials Complexity and Anode Recycling
Managing mixed cathode materials with varying chemical compositions and finding ways to convert them into useful recipes for current batteries remains a critical challenge. While graphite, a preferred anode material, is typically not recycled due to its low added value, the inert nature of graphite and silicon-based anode materials allows for extraction in recycling processes. However, restoring their original structure and performance remains a challenge.
All-Solid-State Battery Challenges
The emergence of all-solid-state batteries promises superior thermal and performance stability, lower costs, and higher energy density. However, the recycling of these batteries is nearly nonexistent. Challenges arise from different solid electrolyte (SSE) compositions and lithium metal anodes, necessitating complex separation processes to extract valuable materials.
Scaling Up Recycling Operations
The expansion of lithium-ion battery recycling from academic research to industrial application faces two significant challenges. The gap between innovative ideas in academia and the complexities of large-scale industrial operations limits the development of recycling technology. Additionally, scaling up to meet the annual output of 2 million tons of global waste lithium batteries by 2030 requires addressing diversity, complexity, lack of regulation, and non-standardization issues in battery designs.
Economic Sustainability Challenges
Economic viability is crucial for the success of lithium battery recycling. The intentional reduction of cobalt, the most valuable element in cathode materials, in new compositions complicates traditional recycling processes. Adapting and optimizing existing technologies becomes necessary to enhance profits and economic feasibility, urging researchers to explore dismantling technologies, classification methods, and recycling design improvements.
Battery Material Requirements and Testing
Persuading large battery manufacturers to incorporate recycled materials into their production lines is a formidable challenge. Rigorous testing is required to ensure recycled materials meet or exceed the performance of raw materials, considering industrial requirements for multi-layer soft-clave batteries. Collaboration between academia and industry is crucial to bridge the gap and align recycling efforts with industrial standards.
In conclusion, addressing these technical, design, material, scaling, economic, and testing challenges is essential for the successful and sustainable recycling of lithium-ion batteries. Overcoming these hurdles will pave the way for a more environmentally friendly and economically feasible approach to handling the increasing volumes of waste lithium batteries.
No responses yet